The efficient operation of reverse osmosis (RO) systems relies on the precise synergy of pretreatment, high-pressure pumps, and membrane modules. This article explores the core components and their collaborative mechanisms, integrating engineering practices and technological innovations.
I. Pretreatment System: The “Lifeline” for Membrane Protection
Pretreatment serves as the first defense line, directly impacting membrane lifespan and desalination efficiency. Key steps include:
Multi-Media Filtration: Removes suspended solids using quartz sand and anthracite, reducing turbidity to <1 NTU.
Activated Carbon Adsorption: Eliminates residual chlorine (<0.1 mg/L), organic matter, and odors to prevent polyamide membrane oxidation.
Softening and Antiscalant Dosing: Adjusts pH to 5–7 with HCl or H2SO4 and inhibits calcium/magnesium scaling using sodium hexametaphosphate (5–20 mg/L).
Cartridge Filtration: A 5–20 μm security filter intercepts residual particles to prevent membrane abrasion.
Innovation: Ultrafiltration (UF) as a novel pretreatment technology removes 99% of colloids and microbes, stabilizing the silt density index (SDI) at <4.
II. High-Pressure Pump: The Energy Core for Pressure-Driven Flow
The pump balances energy consumption and membrane safety:
Pressure Control: Brackish water systems require 6–15 MPa, while seawater desalination demands 55–80 MPa.
Frequency Conversion Technology: Dynamically adjusts pump speed based on influent TDS, reducing energy consumption by 40%.
Anti-Shock Design: Stabilizers and 2–3-minute slow-opening valves prevent high-pressure pulses from damaging membranes.
Case Study: A 10 m³/h system with multistage centrifugal pumps achieves energy consumption of 2.8 kWh/m³ at 5,000 mg/L TDS.
III. Membrane Modules: Intelligent Separation Executors
Membrane configuration determines system recovery rate and stability:
Single-Stage Single-Pass Recycling: Concentrate recirculation increases recovery to 60%, but product water TDS rises by ~15%.
Single-Stage Multi-Pass Series: A 4:2:1 layout maintains terminal concentrate flow velocity >0.3 m/s to mitigate concentration polarization.
Multi-Stage Hybrid Systems: Two-stage RO reduces seawater TDS (35,000 mg/L) to 500 mg/L with a total recovery rate of 45%.
Innovation: Anti-fouling composite membranes (e.g., DOW FILMTEC™ BW30-400) enhance colloidal rejection to 99.9% via surface charge modification.
IV. Synergistic Optimization: Data-Driven System Integration
Key principles for module synergy include:
Water Quality Matching: Pretreatment effluent must meet SDI <4, residual chlorine <0.1 mg/L, and temperature 25±2°C. Pressure Coordination: Real-time calibration between pump pressure and membrane flux avoids overpressure-induced membrane collapse. Smart Monitoring: Online tracking of transmembrane pressure (cleaning triggered at ΔP >20%) and product water conductivity (alarm at desalination rate <98%).
Case Study: An electronics ultrapure water project using “UF + Dual-Stage RO + EDI” achieves 18 MΩ·cm resistivity with a 5-year membrane lifespan.
V. Future Trends: Efficiency and Sustainability Breakthroughs
Energy Recovery: Turbochargers convert concentrate pressure into electricity, reducing energy consumption by 30%.
AI-Driven Operation: Machine learning predicts membrane fouling cycles to optimize chemical cleaning frequency.
Zero Liquid Discharge: Concentrate reuse via evaporation crystallization or ion exchange achieves >95% water utilization.
Conclusion
The essence of RO technology lies in the collaborative interplay of pretreatment, high-pressure pumps, and membrane modules. Innovations—from quartz sand filtration to AI-driven pressure control—continuously enhance energy efficiency and cost-effectiveness. With advancements in materials and automation, RO systems will further dominate seawater desalination and industrial wastewater reuse.
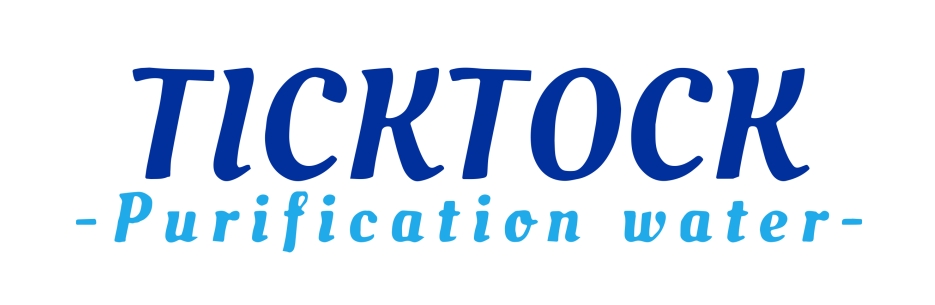