Industrial reverse osmosis (RO) equipment has become a cornerstone of modern water treatment, driven by its high-precision separation and modular design. This article explores breakthrough applications in electronics, pharmaceuticals, chemicals, power generation, and seawater desalination.
I. Electronics Industry: Precision in Ultrapure Water
Semiconductor manufacturing demands ultrapure water with 18 MΩ·cm resistivity. RO systems achieve this through multistage pretreatment + RO + EDI integration:
1. Nanoscale Filtration: Polyamide membranes remove 99.9% of ions and particles (e.g., SiO₂ <0.1 ppb) for wafer cleaning.
2. Chemical-Free Operation: EDI replaces traditional ion exchange, cutting wastewater by 60% and aligning with ISO 14644 cleanroom standards.
Case Study: A 12-inch wafer fab using “dual RO + EDI” produces 500 m³/d of water with 18.2 MΩ·cm resistivity, boosting chip yield by 12%.
II. Pharmaceutical Sector: Sterility Assurance
RO ensures compliance with Chinese Pharmacopoeia standards for Water for Injection (WFI):
1. Endotoxin Control: Membranes block >200 Da contaminants, achieving <0.25 EU/mL endotoxin levels.
2. Closed-Loop Design: 316L stainless steel pipelines and CIP systems prevent microbial contamination.
Case Study: A biopharma plant reduced defective infusion products from 0.3% to 0.02% using RO, saving $300,000 annually in energy costs.
III. Chemical Industry: High-Salt Wastewater Valorization
For wastewater with TDS >10,000 mg/L, RO enables salt separation + ZLD solutions:
1. Salt Recovery: NF-RO hybrids reclaim >85% of NaCl and Na₂SO₄.
2. Zero Liquid Discharge: MVR crystallizers produce 99%-pure industrial salts, achieving 95% resource utilization.
Case Study: A dye plant treats 3,000 m³/d of brine, recovering 12,000 tons/year of sodium sulfate and reducing COD by 150 tons.
IV. Power Generation: Boiler Water Efficiency
RO optimizes boiler feedwater (hardness <1 mg/L) in thermal power plants:
1. Fouling-Resistant Membranes: Dow BW30-400FR withstands 1,000 ppm chlorine, extending cleaning cycles to 6 months.
2. Smart Monitoring: AI predicts scaling risks via SDI and pressure data, cutting maintenance costs by 40%.
Case Study: A 1,000 MW plant improved boiler efficiency by 2.3%, saving 18,000 tons/year of coal.
V. Seawater Desalination: Energy-Efficient Breakthroughs
RO reduces desalination energy from 10 kWh/m³ to 2.8 kWh/m³ via:
1. Energy Recovery: Turbochargers reuse brine pressure, boosting system efficiency by 35%.
2. High-Flux Membranes: Graphene-modified membranes achieve 40 LMH flux, doubling output.
Case Study: Saudi Arabia’s Rabigh III project produces 600,000 m³/d at $0.5/m³, the world’s largest RO desalination plant.
Future Trends: Intelligence & Sustainability
1. AI-Driven Operations: Machine learning predicts membrane fouling, extending lifespan by 30%.
2. Renewable Integration: Solar-powered RO systems in UAE achieve carbon-neutral desalination.
3. Advanced Membranes: Biomimetic nanochannel membranes target >99.99% salt rejection and 3x antifouling performance.
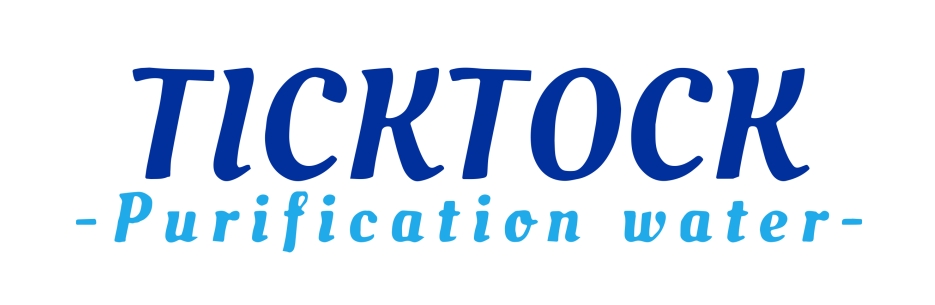